I Decrease your environmental impact with machine control test blog
blog 01 May 2024
Blog Description We can’t escape from the fact that the construction industry makes a huge impact on the environment, from CO2 emissions, to particulates, noise and vibration. We already do our best to monitor this, but what if we can nip those environmental issues in the bud at the source? Our machines.
Sunbelt Rentals UK supply smaller electric machines such as dumpers, and excavators up to 2.5T, but the problem is the large excavators. Although our stage V plant can help significantly reduce tail pipe emissions, large plant is still a high consumer of fuel, and our largest excavators can pump out CO2 emissions at an alarming rate – with some averaging 16 tonnes per year*. Though fuel options available such as biodiesels are available, which alongside being a sustainable diesel alternative is also low emission, it still does produce those emissions.
We also do our best to increase fuel efficiency: reducing idle time, training our operators to high standards, selecting the right machine for the job. Electric and hybrid plant are good options – but even electricity has a carbon footprint. So, then what? The solution, we think, lies in the amount you use the machine in the first place. Wouldn’t it benefit your project and your fuel emissions to spend less time on that work?
Enter machine control solutions.
Machine control uses 3D design models of your project to enable operators to accurately position earthwork machinery, allowing for precise digging and grading. Multiple sensors are fitted to the machine to track movement, and a machine control panel is fitted inside the cabin, displaying the model and allowing the operator to see, in real time, how close their work is to the design. Using this technology, operators can dig once and get the results that you want – the first time, every time.
We worked with Tough Construction, a groundworks contractor, to deliver a full project solution with machine control – we provided the equipment, installed it in their plant machines, provided training and gave full technical support. The results speak for themselves, with a minimum of 4 hours being saved while digging foundations alone. On a 100-home development, this would be a time saving of 400 hours. For foundations, the operator takes less times to follow a screen than to decipher marks on the ground, there is no requirement for a second person to check the dig level, or for an engineer to spend time calculating coordinates for the foundation on site.
The company have since gone on to use machine control across their projects, discovering time and cost savings on drainage runs, cut and fill operations, and roads. For roads, there is no requirement for an engineer to visit site to set up profiles, or for a groundworker to use a traveller to construct the road. Weeks are saved on cut and fill operations, as there is no requirement to profile the ground, use travellers, no remediation and no risk of finished levels being incorrect. With the introduction of machine control, Tough Construction were able to complete a 50,000m cut and fill operation 2 months ahead of schedule, with no additional labour.
So, when using machine control, you can spend less time on the job itself, increasing your productivity, and reducing your costs, and less time with the engine running or idle. That can mean a huge decrease in fuel consumption and therefore lower carbon emissions.
Title
Title
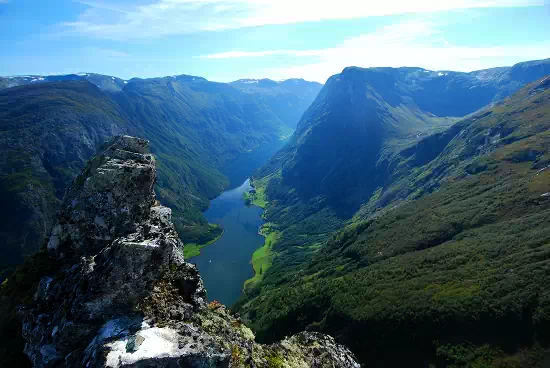